How To Select The Best Cutting Tools For PCD?
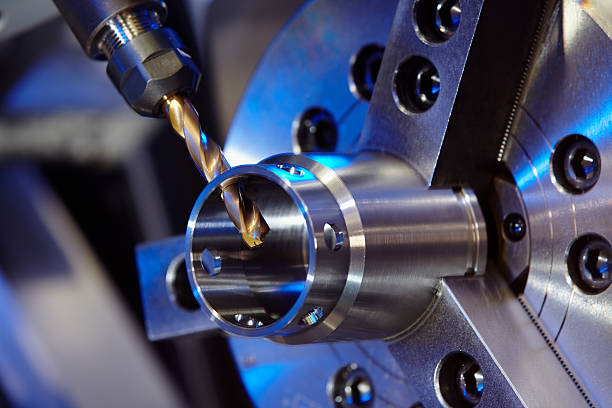
You're probably thinking about how to choose the right PCD cutting tools to
suit your needs. Continue reading to learn about the fundamental characteristics
of PCD cutting tools and their applications. After that, you can get started on
edge preparation. You'll ultimately get the results you're looking for. These
are the primary elements to think about when choosing solid
cbn inserts for hard turning. After all, your performance at work is
dependent on it.
The best pcd cutter tools
Although PCD devices are more costly than other carbide materials in terms of
price, they offer greater accuracy and longer tool life as compared to carbide
cutters. PCD tools can enhance the efficiency of carbide tools however, a PCD
cutter is not the only option. It is crucial to think about the cost-benefit
ratio with respect to the machining process. An in-depth understanding of the
product and the procedure is necessary to minimize mistakes and maximize
productivity.
PCDs are more adaptable than other types of materials, such as carbide. For
instance, aluminum-based products are becoming more common in the automotive
industry, and pcd reamer manufacturer is a common option for these parts.
However, you should not make use of them on ferrous materials. If you have
specific requirements TOMMASIN UTENSILI can provide specific PCD tools. These
cutting tools are employed on complex, intricate parts.
Specifications
PCD cutting tools offer a variety of advantages. They offer a long-lasting
durability as well as a stable dimensional accuracy and good surface roughness.
The most important processing components are woodworking materials, ceramics and
alloys. Moreover, the pcd
tool can process various composites made of fiber and an array of metal alloys.
There are three types of cutting tools for PCD available such as hub cutters,
inserts, and piston series cutters.
We carried out several tests to examine the wear characteristics of PCD
tools. We employed two grinding techniques to make a three-dimensional PCD
device and then tested them using high-speed cutting of titanium alloy. The
purpose of this study was to study the cutting force and geometry, worn
morphology, and wear mechanism of PCD tools. The results of this work will allow
us to improve the design of PCD cutting tools.
Applications
In creating a product that demands precision and high efficiency the company
should use the right PCD cutting tools. Cutting tools for PCD are manufactured
by rigorous design and engineering processes. Built with the highest quality in
mind, they provide longer tool lifespan and greater throughput, while delivering
an affordable cost of ownership. The best PCD cutter tools will lower the cost
of your final product, without sacrificing quality and productivity.
Be sure to take into account the material you're cutting when selecting the
appropriate PCD cutter tools. Tools made of carbide, for instance, can quickly
wear out and require frequent tool adjustments. Additionally, non-ferrous
materials like fiberglass and copper require PCD tooling. Furthermore, they
maintain sharp cutting edges longer, which makes them suitable for a range of
uses. PCD inserts are a great option if you need a tool that is able to endure
high temperatures.
Edge preparation
When choosing PCD cutting tools It is crucial to understand the role that the
edge preparation play. Edge preparation is essential for the success of
manufacturing and also for cutting tools to perform at their optimal levels.
Edge preparation is an integral part of every manufacturing process pcd reamer
manufacturer. But, how do you determine what tools are best suited to the
requirements of your particular situation? For more information learn more!
Let's first define what edge preparation means.
Carbide drills can be difficult to prep. It can involve t-land and grinding. PCD prefers edge preps as well as organized hones. These can be expensive and differ in size based on the particular tool. PCD is generally operated "up sharp." This is contingent on the manufacturer. Certain suppliers have tested their PCD tools 10,000 times before being considered to be sharp.
Comments
Post a Comment